Fabrication The Mosaic Centre
August 5, 2014
Now that we’ve introduced The Mosaic Centre, let’s take a closer look at the fabrication process that ultimately yields the curtain wall sections used in this landmark project. Before GlasCurtain is installed on-site, the curtain wall system has to be made-to-measure from stock fiberglass lengths.
Known as “lineals,” the fiberglass lengths are sent from our fabrication facility in Winnipeg to our glazing contractor partner, in this case Ferguson Glass in Calgary. There, the lineals are taken through a precise series of steps to turn them into useable curtain wall frames.
Let’s have a look at how the fabrication happens!
First, The fiberglass lineals arrive and are unpackaged, each being inspected for damage incurred during transport.
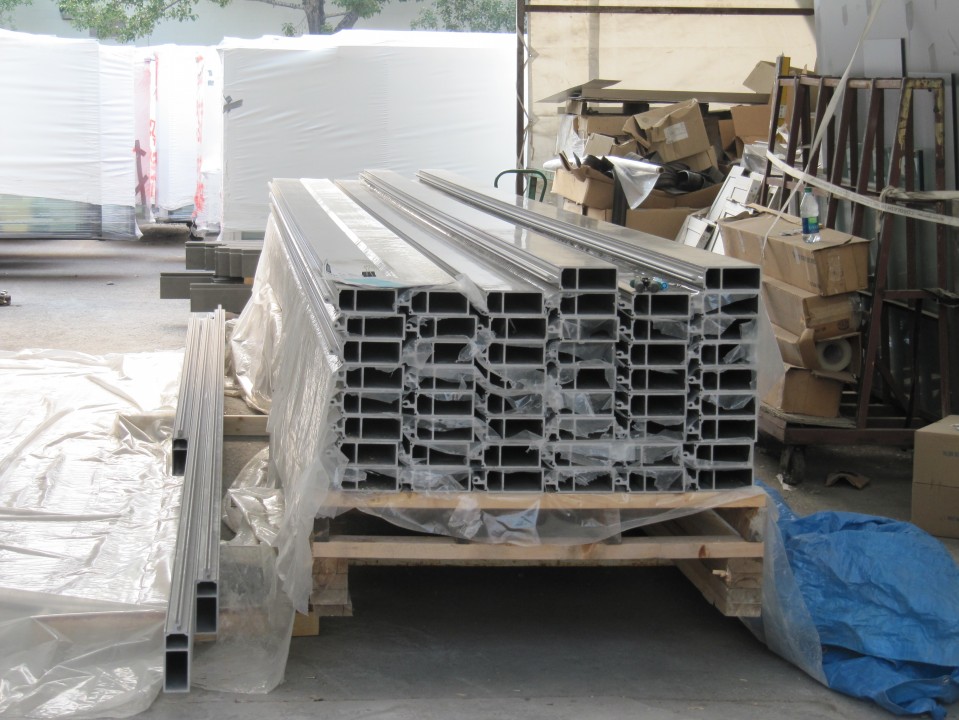
Using the shop drawings as a guide, the stock lineals are cut with a special diamond blade to their final length.
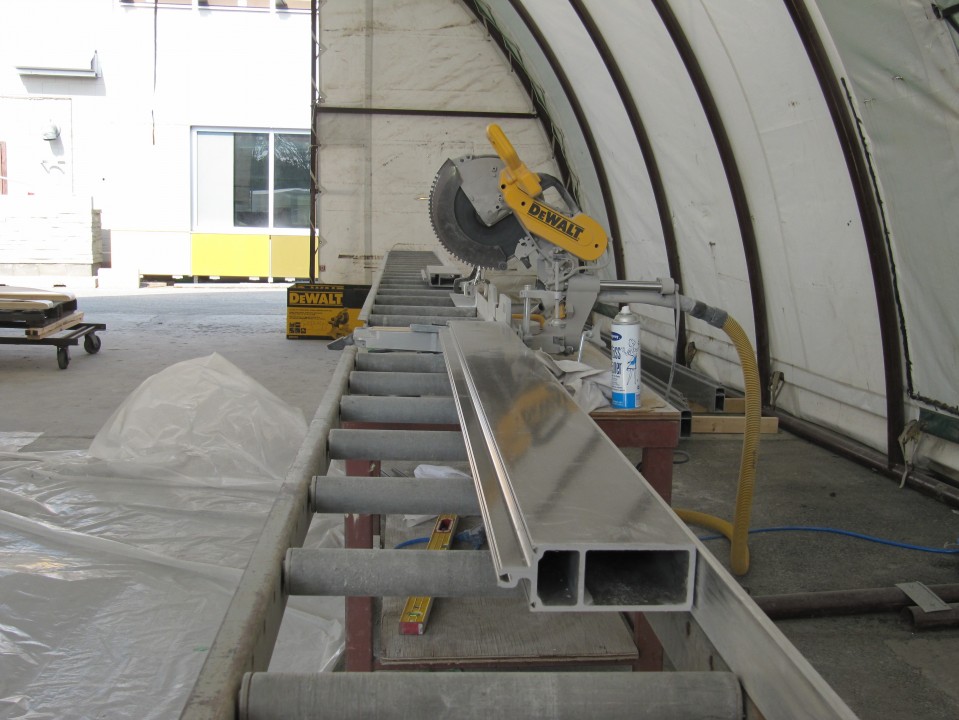
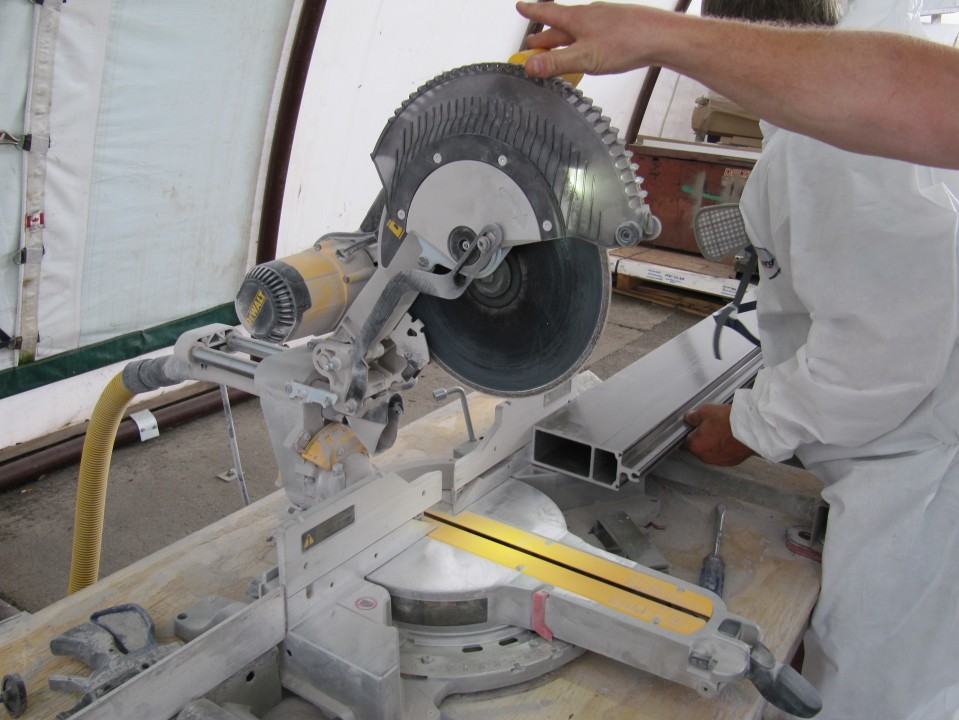
The cut lineals are then organized in the shop.
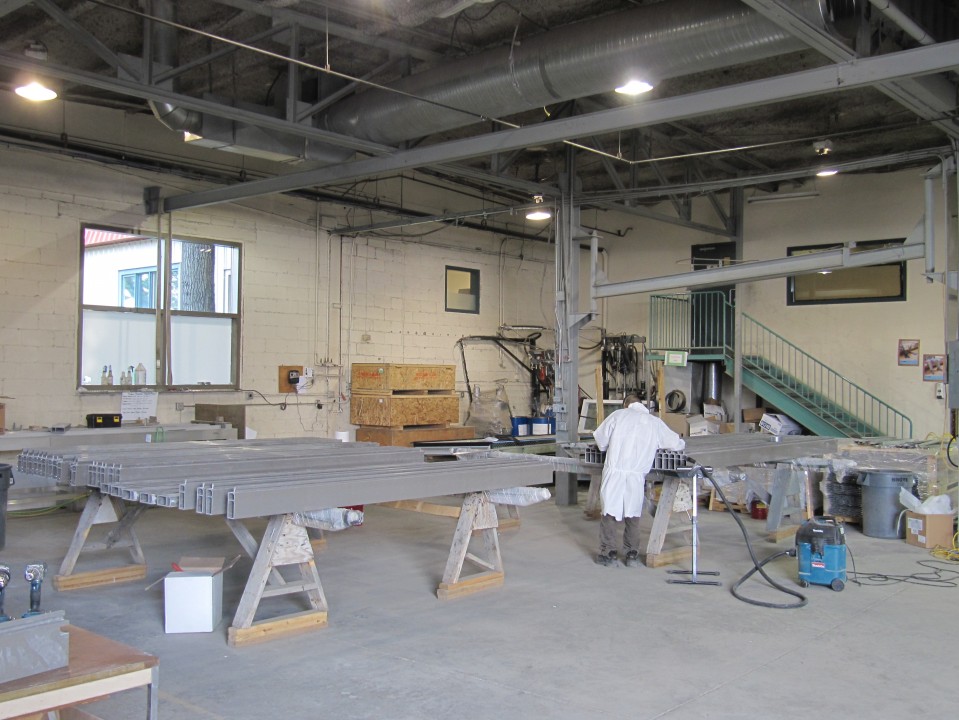
Once in the shop, the first step is to cut a corner of the profile off so that the vertical and horizontal sections fit snuggly against one another.
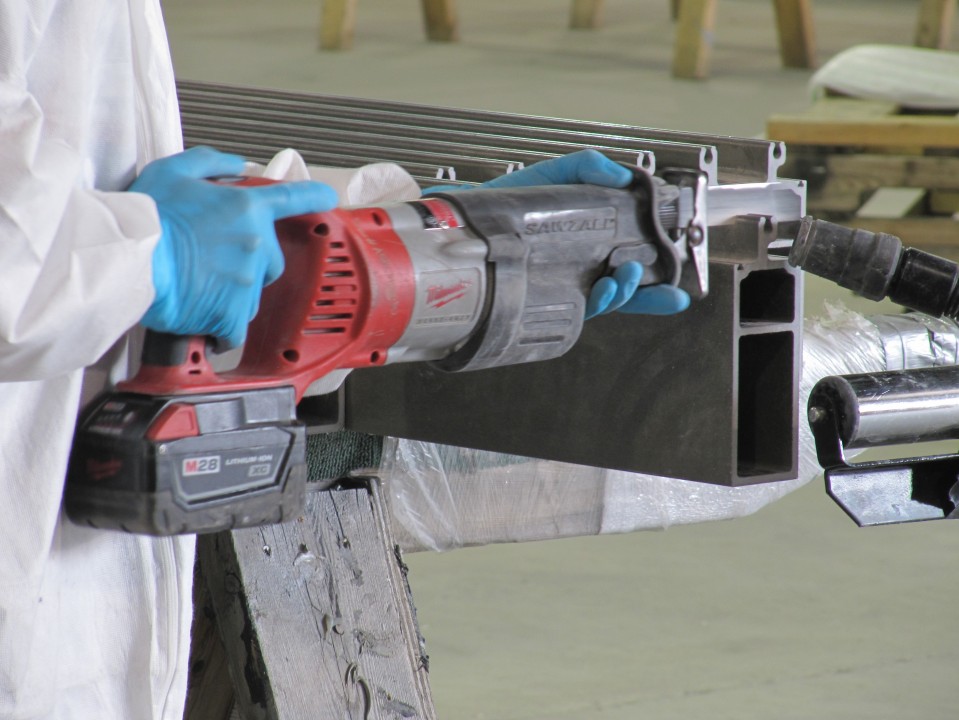
Next, the sheer blocks, also known as “spigots,” are installed. To do so, holes are first drilled into the fiberglass mullion using a special diamond drill bit.
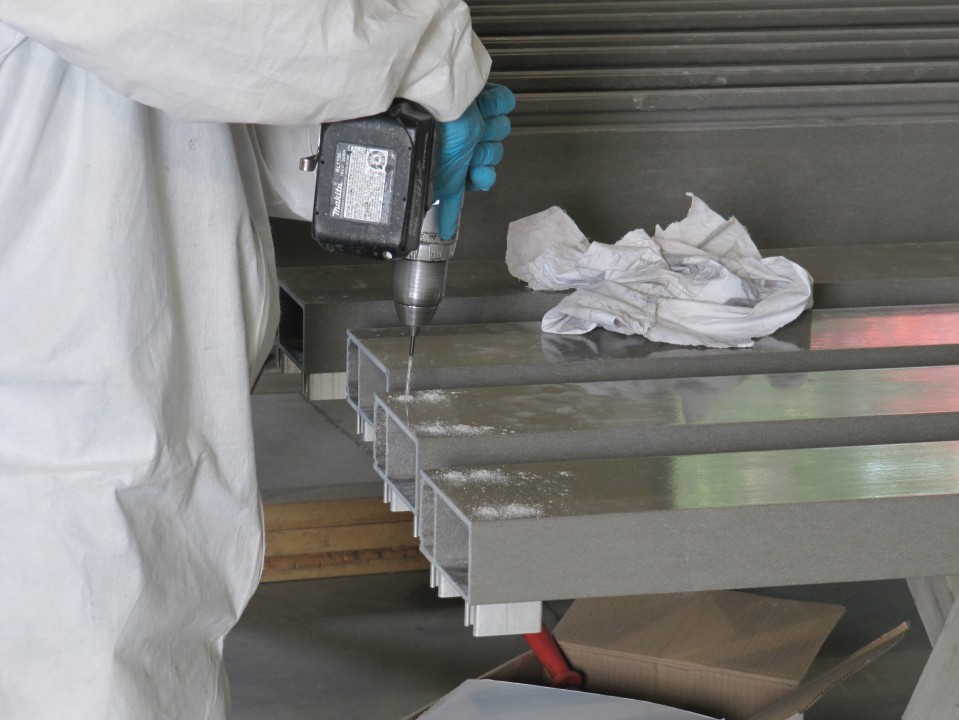
Then, the sheer blocks are screwed into place.
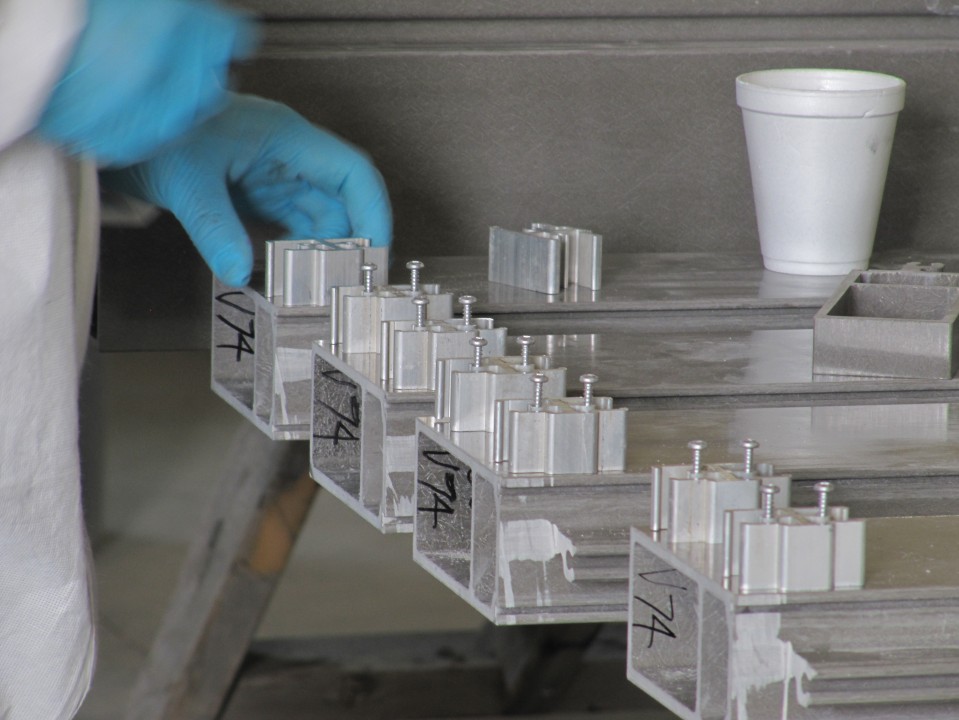
Following this, the nosing, seen below before installation, is glued into the channel in the fibreglass profile. The nosing bears the screw that attaches to the pressure plate, which is also made of fibreglass composite. Although the nosing is aluminum, that it’s surrounded by fibreglass means that it doesn’t act like a thermal bridge in the way that traditional curtain wall systems do. This difference is what gives GlasCurtain its distinct thermal performance advantage.
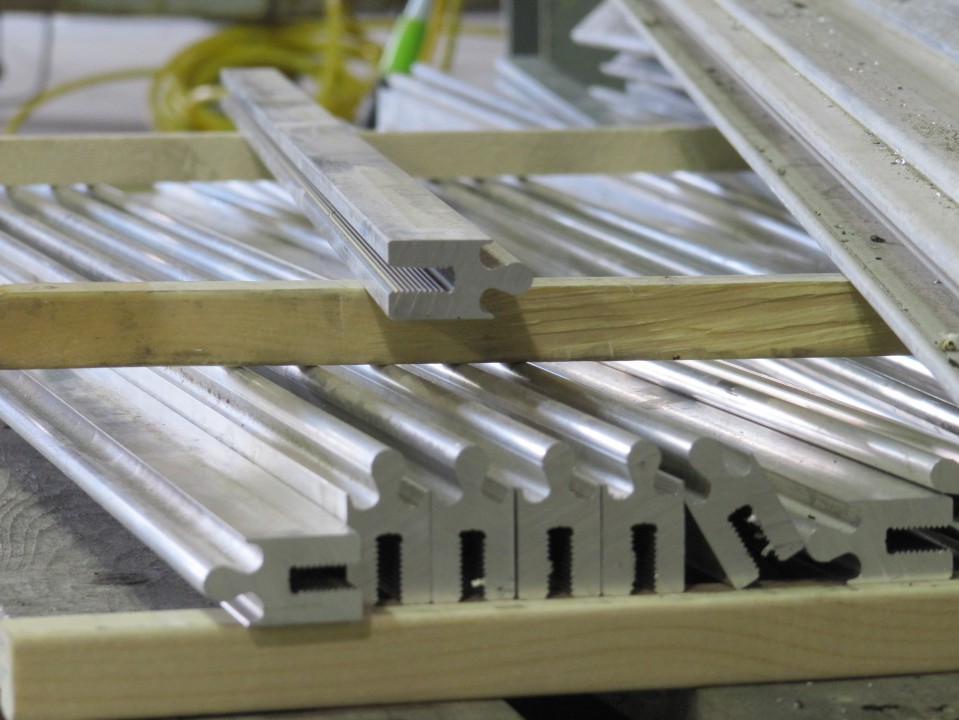
Glue is applied into the fibreglass channel.
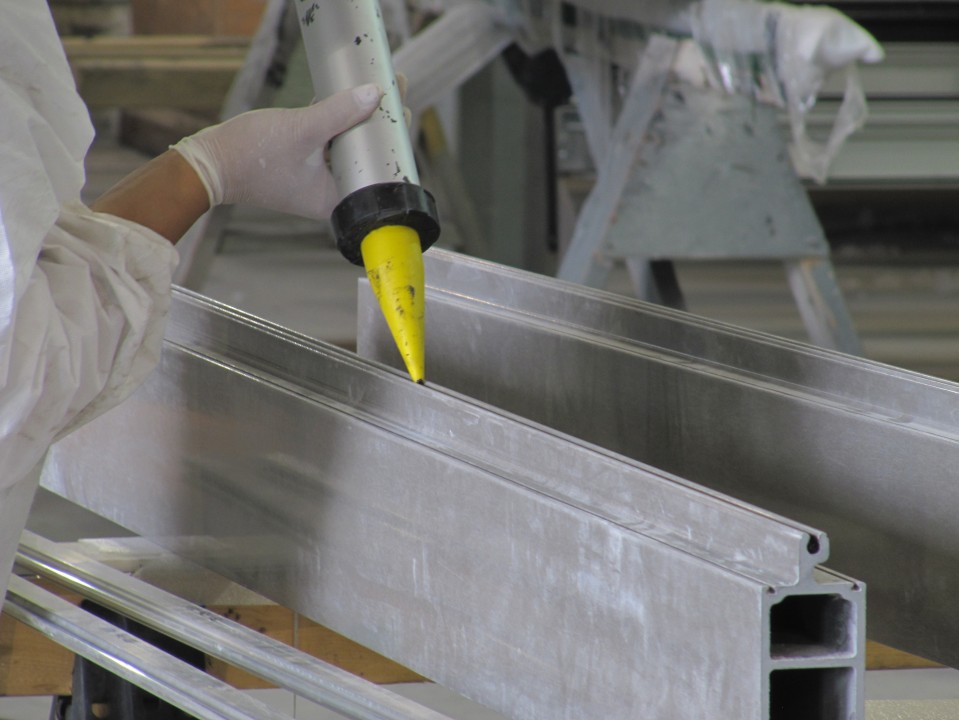
Then voilà!
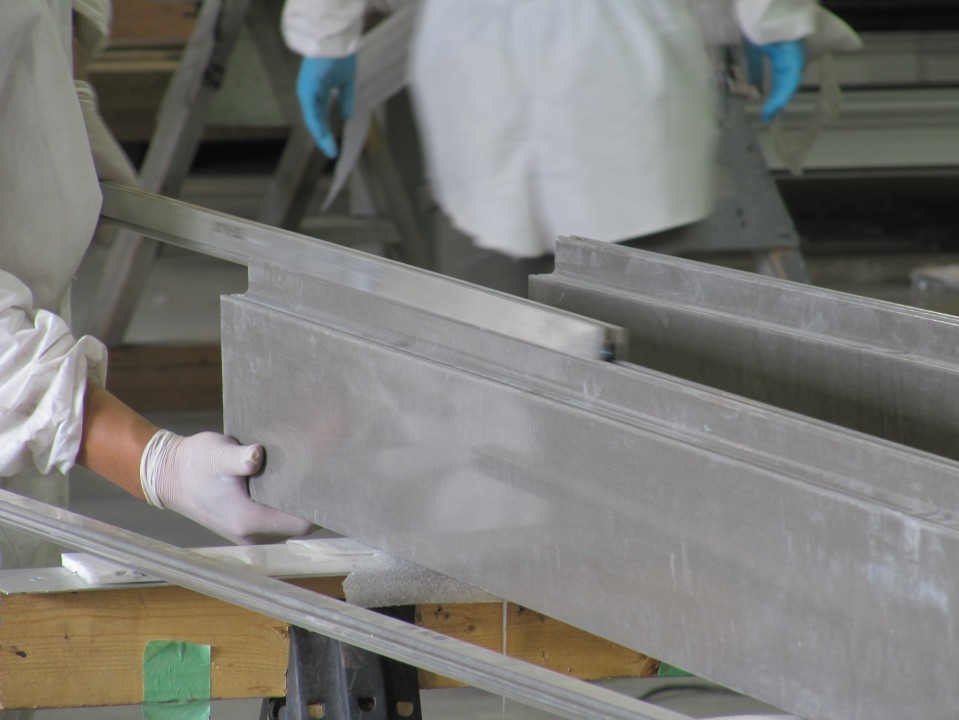
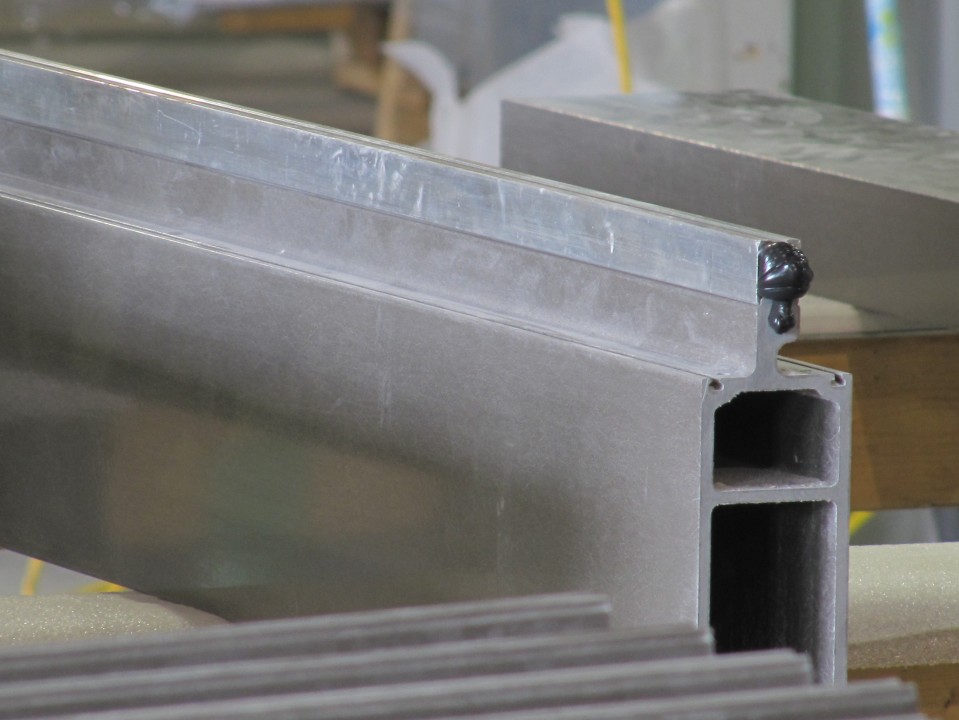
Once all the pieces are completed, everything is inspected one last time.
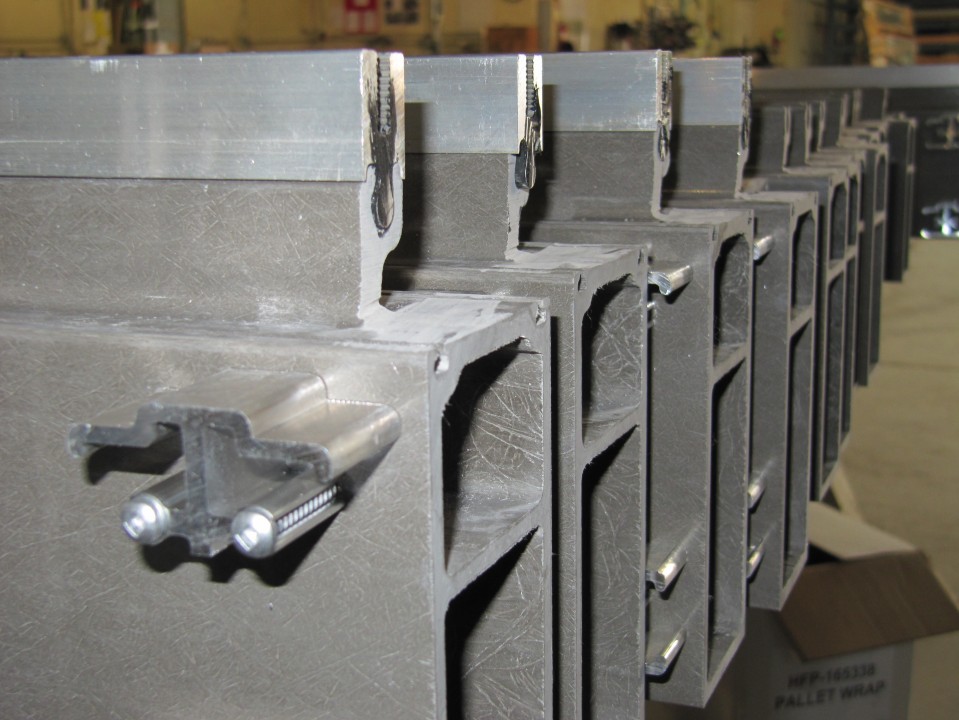
Once everything is good to go, the completed framing sections are packaged, numbered, and stored in the loading bay until they’re picked up and shipped to the construction site.
While the completed sections seen below aren’t the longest spans on the project, The Mosaic Centre will actually use vertical GlasCurtain spans as long as 8.4m in length, meaning that no vertical stacks are required for the building’s atrium. While traditional curtain wall can in theory span similar lengths, in practise, aluminum spans are often limited to 6.0m due to the size of the anodizing tank. Since fibreglass is, by its material nature, corrosion-resistant, anodizing isn’t required and spans are limited by structural strength, which, we already know, is pretty darn impressive.
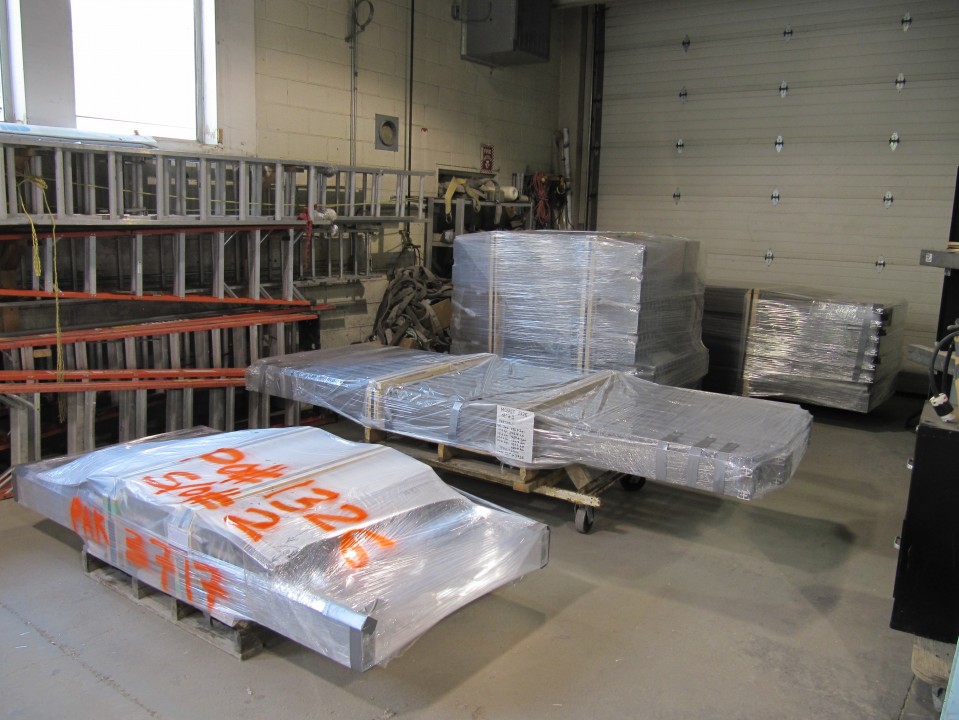
Thus concludes the curtain wall fabrication process.
Next up: on-site installation in Edmonton!